Worm Gear Design Calculation Pdf Printer
The following is a calculation for the Reference Diameter of a helical gear with transverse module mt = 2, Number of teeth z = 30, Helix angle β = 15° (R) Reference Diameter d = z mt = 30 × 2 = 60 The following is a calculation for the Reference Diameter of a helical gear with normal module mn = 2, Number of teeth z = 30, Helix angle β = 15° (R).
Input Parameters
Teeth type - common or spiral
Gear ratio and tooth numbers
Pressure angle (the angle of tool profile) α
Module m (With ANSI - English units, enter tooth pitch p = π m)
Unit addendum ha*
Unit clearance c*
Unit dedendum fillet rf*
Face widths b1, b2
Unit worm gear correction x
Worm size can be specified using the:
- worm diameter factor q
- helix direction γ
- pitch diameter d1
Auxiliary Geometric Calculations |
Calculated parameters
Common gearing ZN
Axial module | mn = m |
Normal module | mx = mn cos γ |
Axial pressure angle | αx = a |
Normal pressure angle | αn = arctg (tg α cos γ) |
Helix/lead angle | γ = arcsin z1/q |
Spiral gearing ZA
Axial module | mn = mx / cos γ |
Normal module | mx = m |
Axial pressure angle | αn = arctg (tg α cos γ) |
Normal pressure angle | αx = α |
Helix/lead angle | γ = arctan z1/q |
Normal tooth pitch
Axial tooth pitch
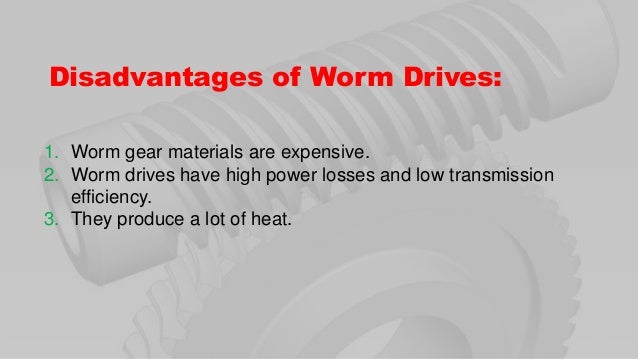

px = πx |
Basic tooth pitch
Lead
Worm Gear Design Calculator
pz = z1 px |
Virtual/alternate number of teeth
Helix angle at basic cylinder
sin γb = sin γ cos αn |
Worm pitch cylinder diameter
Worm gear pitch circle diameter
d2 = z2 mx |
Worm outside cylinder diameter
Worm gear outside circle diameter
da2 = d2 + 2m (ha* + x) |
Worm root cylinder diameter
Worm gear root circle diameter
df2 = d2 - 2m (ha* + c* - x) |
Worm rolling(work) circle diameter
Worm gear rolling(work) circle diameter
dw2 = d2 |
Worm gear root circle diameter
Center distance
Chamfer angle of worm gear rim
Worm tooth thickness in normal plane
Worm gear tooth thickness in normal plane
Worm tooth thickness in axis plane
sx1 = s1 / cos γ |
Worm gear tooth thickness in axis plane
Work face width
bw = min (b1, b2) |
Contact ratio
εγ = εα + εβ
where:
Minimum worm gear tooth correction
where:
ha*0 = ha* + c* - rf* (1 - sin α) | |
c = 0.3 | for α = 20 degrees |
c = 0.2 | for α = 15 degrees |